الکترود مادهای رسانا است که از یک سو به بخش فلزی (مانند سیم مسی) و از سوی دیگر به بخش غیرفلزی (نیمهرسانا، الکترولیت و یا خلأ) مدار الکتریکی متصل شده و بین آنها ارتباط برقرار می کند.
الكترود جوشکاری مفتول فلزی است که دور تا دور آن توسط پوشش فلاکس ( (Flux Coating احاطه گردیده است. قطر آن از روی قطر مغزی آن محاسبه می گردد. روکش الكترود اغلب از آهک، سلولز، اکسید سدیم، خاک رس و یا آزبست تشکیل گردیده است. از الكترود جهت پرکردن فضای اتصال مابین دو سطح مورد جوشکاری استفاده می گردد
پوشش فلاکس
پوشش فلاکس الکترود کمک زیادی به ثبات قوس الکتریکی می کند. همچنین ضمن عمل به عنوان عایق جهت ایجاد گاز محافظ (Gaseous Shield) و شکل گیری سرباره (Slag) شناور بر روی سطح برای افزایش مدت زمان خنک شدن جوش مورد استفاده قرار می گیرد.
انواع الکترود از لحاظ جنس مفتول:
- الکترود با مفتول فولاد زنگ نزن
- الکترود با مفتول فولاد کم کربن
- الکترود با مفتول نیکلی
- الکترود با مفتول آلومینیومی
انواع الکترود از نظر پوشش فلاکس:
- الکترود پوشش قلیایی
- الکترود روتیلی
- الکترود روتیلی با پودر آهن
- الکترود سلولوزی
انواع الکترود از لحاظ ضخامت پوشش:
- الکترود پوشش تازک
- الکترود پوشش متوسط
- الکترود پوشش ضخیم
- الکترود پوشش خیلی ضخیم
انواع الکترود:
انجماد سریع (Fast Freezing Electrode):
الکترود های جوشکاری انجماد سریع دارای سه خصلت اصلی هستند. ضمن ایجاد قوس قوی، سرباره بسیار کمی تولید می کنند و امکان استفاده در تمام موقعیت ها را دارند. کدهای E6010 و E6011 از انواع الکترود های انجماد سریع هستند.
انجماد پرشده (Fill Freeze Electrode):
الکترودهای جوشکاری انجماد پر شده دارای فلاکسی سنگین بوده و ضمن توانایی خارج کردن سرباره، امکان ایجاد دانه هایی با ترکیب یکنواخت را نیز دارند. کدهای E6012، E6013 و E7014 در ذمره الکترود های انجماد پر شده قرار می گیرند.
چسبان سریع (Fast Fit Electrode):
الکترود های جوشکاری چسبنده سریع دارای پوشش فلاکس بسیار سنگین بر روی سیم و نرخ رسوب گذاری بسیار سریع هستند. کدهای E6027، E6028 دو نوع از پرکاربردترین هستند.
کم هیدروژن (Low Hydrogen Electrode):
فلاکسی الکترودهای کم هیدروژن دارای مقادیر بسیار کمی هیدروژن می باشد و از آن برای فولادهای پرکربن استفاده می گردد. E7018 و E7028 در ذمره الکترودهای کم هیدروژن هستند.
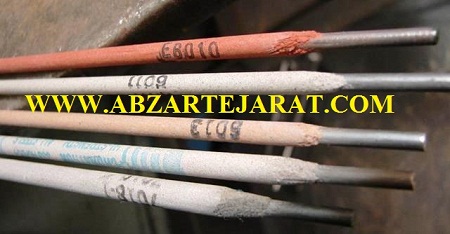
ضخامت الکترود و آمپر:
در اغلب موارد هرچقدر قطعه کار ضخیم تر باشد، جریان و آمپراژ مورد نیاز بیشتر و ضخامت الکترود نیز بیشتر خواهد بود. کاتالوگ سازنده می تواند اطلاعات مفیدی در خصوص انتخاب مناسب و تنظیمات دستگاه جوش در اختیار جوشکار قرار دهد.
الکترودهایی که در جوش اتصال فولاد به کار برده می شوند مفتولهای مغزی با آلیاژ یا بدون آلیاژ دارند که جریان جوش را هدایت می کند. شعله برق بین قطعه کار و سرآزاد الکترود می سوزد و الکترود به عنوان یک ماده اضافی ذوب می شود
الکترودهای نرم شده دارای علائم اختصاری بوده ( دین 1913 ) که روی بسته بندی آنها نوشته شده است. علائم اختصاری تمام نکات مهمی که در به کار بردن آن الکترود باید مراعات شوند نشان می دهند
اصول حاکم بر انتخاب الکترود
جوش حاصل از الکترود باید از نظر مقدار ونوع عناصر، حداقل با فلز پایه برابری کند .
به غیر از الکترودهای سخت پوشی کربن الکترود باید از 0.15% وزنی کمتر باشد .
برای فلزات با کربن معادل بالای 0.35% فقط مجاز به استفاده از الکترودهای قلیایی هستیم .
برای موارد ضخامت بالا باید برای افزایش سرعت جوشکاری و کاهش تنشهای پسماند از الکترودهای باجایگزینی بالا استفاده نمود .
فولاد ها
- درصد عناصر آلياژي =0(ساده كربني - plain carbon steel
- درصد عناصر آلياژي ≥1 ( ميكرو آلياژي - steel micro alloy
1≥ درصد عناصر آلياژي ≥ 5 (كم آلياژي - low alloy steel
5≥ درصد عناصر آلياژي ≥50 (پر آلياژي - high alloy steel
انواع فولاد ساده كربني
درصد كربن ≥ 0.1% (كم كربن - low carbon steel
0.1 ≥ درصد كربن ≥ 0.3 ( نرم (كربني ) - steel mild
0.3≥ درصد كربن ≥ 0.6(كربن متوسط - medium carbon steel
0.6≥ درصد كربن ≥1.7 (پر كربن - high carbon steel
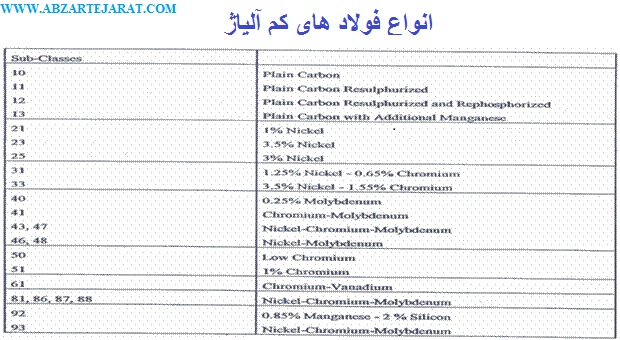
جدول ذیل جهت انتخاب الکترود از استاندارد برای شما نمایش داده شده
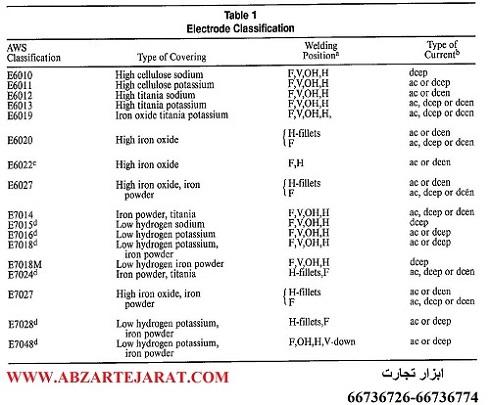
اثرات عناصر آلیاژی اصلی در فولاد
منگنز: استحکام بخشی – تافنس زایی – حذف اثرات مخرب گوگرد
کروم: افزایش مقاومت به اکسیداسیون و خوردگی - استحکام بخشی
مولیبدن: افزایش مقاومت به خزش - تافنس زایی
نیکل: تافنس زایی به ویژه در دماهای پایین – مقاومت به خوردگی
وانادیوم: تافنس زایی
ترکیبات شیمیایی را در الکترودها در جدول ذیل دریابید
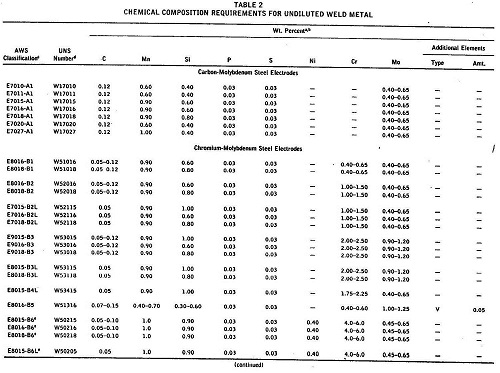
فولادهای کم کربن ساختمانی
مهمترین فولادهای این گروه عبارتند
ST 37- ST44- ST12- CK10- CK20
مناسبترین الکترود برای ضخامت های کمتر از 1 اینچ
E60XX
وبرای ضخامت بالای 1 اینچ سری
E70XX
فولادهای کربن متوسط
این نوع فولاد ها ناقل بار میباشند.معروف ترین این فلزات
CK35 ,CK45
برای جبران کاهش کربن جوش، مناسب ترین گزینه گروه الکترودهای
استفاده E80XX میباشدو دربعضی موارد نیزازE70XX
برای خال جوش زدن نیز بهتر است از الکترودهای نیکلی و یا زنگ نزن آستنیتی استفاده نمود مانند
ENiFe-C1, E308, E309
فولاد های پرکربن
این فولادها مقاوم به سایش بوده و معروفترین کدهای آنها عبارتند از
CK60-CK75,CK100
برای جبران کاهش کربن جوش بهترین گروه ازالکترودها
E100XX-D
فولادهای منگنز دار
این فولادها در مواردی که استحکام و تافنس بالا مد نظر باشد جایگزین فولادهای ساده کربنی می شوند. معروفترین فولادهای این گروه عبارتند از:
30Mn5- 40Mn4- ST52- A515- A516
مناسبترین الکترود این گروه الکترودهای
E70XX-C ,E70XX
فولادهای نيکل دار
این فولادها مناسب برای کاربرد در دمای پایین می باشند معروفترین کد این گروه عبارتنداز
A353-A553-2120-2320
فولادهای کروم - نیکل - مولیبدن دار
این فولادها زمانی که به بالاترین سطح استحکام و تافنس نیاز می باشد مورد استفاده واقع می شوند. معروفترین کدهای این گروه عبارتند از
4340,4330,VCN150,VCN200
مناسبترین الکترود جوشکاری این آلیاژها
میباشد.E110XX-M, E120XX-M, E140X
مشخصات الکترودها
در جوشکاری مشخصات الکترودها با یک سری اعداد مشخص می گردند. اعداد مشخصه به ترتیب زیر می باشد
E = جریان برق 60 = کشش گرده جوش بر حسب پاوند بر اینچ مربع 1 = حالات مختلف جوشکار ی 0 = نوع جریان می باشد.
علامت اول
در علائم الکترود بالا E مشخص می نماید که این الکترود برای جوشکاری برق بوده با استقاده می شود. ( بعضی از الکترودهای پوشش دار هستند که در جوشکاری با اکسی استیلن از آنها استفاده می شوند مانند FC18 ).
در علامت دوم
عدد 6 و 0 یعنی مشخصه فشار کشش گرده جوش بر حسب پاوند بر اینچ مربع بوده بایستی آن را در 1000 ضرب نمود یعنی فشار کشش گرده جوش این نوع الکترود 60000 پاوند بر اینچ مربع است. Kg/mm2
علامت سوم
حالات جوش را مشخص می کند که همیشه این علامت 1 یا 2 یا 3 می باشد. الکترودهائی که علامت سوم آنها 1 باشد در تمام حالات جوشکاری می توان از آنها استفاده کرد. و الکترودهائی که علامت سوم آنها عدد 2 می باشد در حالت سطحی و افقی مورد استفاده قرار می گیرند. الکترودهائی که علامت سوم آنها 3باشد تنها در حالت افقی مورد استفاده قرار می گیرند
انواع الکترود برای جوشکاری در تمام حالات مخصوصاً سربالا
استاندارد آما 1/421 م ج رنگ شناسائی : انتها - سورمه ای سیر الکترود روتیلی روپوش متوسط برای فولادهای ساده در تمام حالات مخصوصاً جوش سربالا و بالاسر و حالات اجباری، دارای اکسید آهن. دارای گواهی از لویدز ژرمن جوش دادن با این الکترود بسیار آسان است و سرباره آن بخوبی پاک می شود - قوس آرام دارد - گرده جوش تمیز است و حالات مختلف را با شدت جریان ثابت بخوبی جوش می دهد.
انواع الکترود برای جوشکاری در تمام حالات مخصوصاً سربالا
ستاندارد آما 1/421 م ج استانداردآمریکائی: AWS.E 6013 رنگ شناسائی : انتها - زرد الکترود با روپوش متوسط روتیلی برای جوشکاری فولادهای معمولی در ساختمان اسکلت های فلزی - خرپاها - پل سازی - در و پنجره سازی - ورق کاری و سایر کارهای آهنی - این الکترود را می توان برای جوشکاری درهمه حالات ( عمودی - افقی - و بالاسر ) استفاده نمود. محل جوش نرم است و بخوبی قابل براده برداری یا چکش کاری می باشد. دارای گواهی از لویدز ژرمن و دانشکده پلی تکنیک تهران و هنرستان صنعتی تهران.
انواع الکترود مخصوص جوشکاری مخازن - ماشین سازی - پل سازی و کشتی سازی
استاندارد آما 4/1 + 50 ک ج استانداردآمریکایی: AWS.E 7018/8018 رنگ شناسائی : انتها - نقره ای
الکترود قلیائی برای کارهائی که به جنس جوش فشار زیاد وارد می شود مانند مخازن دیگها - مصارف ماشین سازی - کشتی سازی - پل سازی و بناهای فولادی - قابل کار روی فولادهای ساختمانی ، 33 St ، 34 St ، 42 St ، 50 St ، 52 St ، 60 St ، 70 St و فولادهای دانه ریز با مقاومتهای 50 تا 62 کیلوگرم مثل فولادهای 50 Fb ، 50 Hsb ، 4 Mn 19 ، 5 Mn 17، 39 Bh ، 154 Dillinal ، 50 Aldur ، F 38 Sb ، 6 Fk ، 50 Hoag ، 36 Union ، 36 Bh ورقهای دیگ سازی HIII ، HII ، HI ، ورقهای لوله سازی ، 4/55 St ، 55 St ، 8/45 St ،5/45 St ، 45 St ، 8/35 St ، 35 St ، 4/35 St ، 35 St ، و فولادهای کشتی سازی A . B .C . D .E و فولادهای مقاوم در سرما N 35 TT St ، N 45 TT St ، N 45 TT St ، V 41 TT St ، N 41 TT St ، V 35 TT St و فولادهای مقاوم در کهنگی و سرما. دارای گواهی از خط آهن دولتی آلمان فدرال و لویدزژرمن برای فولادهای ، 50 St ، 60 St ، 70 St
آزمایش شده از طرف اتحادیه مراقبتهای فنی آلمان تا منهای 80 درجه سانتیگراد.
این الکترود با پاشیدن متوسط در همه حالات به آسانی جوش می خورد. فقط الکترودهای خشک مصرف شود. با قوس کوتاه جوشکاری شده و حتی المقدور کمتر نوسان دهند. سربار آن به آسانی پاک می شود. مخصوصاً ثبات فرم آن حتی در حرارتهای کم و تنشهای نامناسب جالب توجه است.
الکترودهای مخصوص رنده های ماشین تراش و صفحه تراش یا فولادهای تنه بر
عملیات حرارتی
الف- تاباندن 5 ساعت در 820 درجه سانتیگراد ب- آب دادن : حرارت سردکردن 1280 تا 1320 درجه سانتیگراد وسیله سردکردن : روغن - حمام گرم - هوای خشک فشرده حرارت حمام کردن : 500 تا 550 درجه سانتیگراد حرارت رنگ گیری : 560 تا 580 درجه سانتیگراد
نمونه مصرف
رنده صفحه تراش طبق دین 4552 __ ساختمان یک رنده صفحه تراش نوبا :__
این فولاد بهتر از همه است زیرا دارای تمام خواص جوشکاری و آبدهی می باشد. حتی المقدور از مصرف فولادهائی که بیش از 45/0 % و کمتر از 35/0% کربن دارند اجتناب شود.
طرز کار
الف- گرم کردن سریع 600 تا 700 درجه سانتیگراد ب- جوش دادن د- سائیدن مقدماتی ( در صورت تاباندن جهت نرم شدن عملیات براده برداری هم ممکن است) هـ - آب دادن در حرارت 1280 درجه سانتیگراد ( در روغن ) و- رنگ گیری نیم ساعت در 560 درجه سانتیگراد ز- به اندازه سائیدن
برای محدود کردن جوش روکشی قطعاتی از مس یا فلزات سبک و همچنین قطعات گرافیت پهلوی آن قرار می دهند. این قطعات کار جوش را آسان کرده و سرعت کار را زیاد می نماید.
قطعات فوق باید طوری باشند که جلوی جریان جوش را نگیرند.برای این منظور یا باید یخ خورده باشند ( 45 درجه ) و یا بین قطعات و قطعه کار 2 تا 3 میلیمتر فاصله باشد.
انتخاب قطر الکترود بسته به سطحی است که باید روکش شود.
آما 1105
رنگ شناسائی : انتها - زرد با خال نقره ای استاندارد :آمریکائیE FE.5B
مخصوص تهیه و اصلاح لبه های افزارها مثل رنده های ماشین تراش و صفحه تراش.
آما 1105 می تواند در تهیه کارهای نو روی فولادهای ساده و در کارهای اصلاحی روی تمام افزارهای فولاد تندبر روکشی شود.
این الکترود دارای قوس آرام است و آسان هدایت می شود جنس جوش متراکم و بدون خلل و فرج بوده سخت و پر مقاومت می باشد و عملیات حرارتی لازم ندارد ولی به هر صورت با آن عملیات سخت تر خواهد شد.
جنس جوش در هر حال قابل براده برداری نیست و فقط ممکن است با سنگ سمباده سائیده شود. در جوش روکشی به روی فولاد کربن دار وقتی بهترین نتیجه حاصل می شود که به فلز مبنا حداقل حرارت لازم جهت چسبیدن جوش برسد. برای این منظور باید حتی المقدور با جریان کم جوشکاری کرد و الکترود را نوسان نداد. فلز مبنا باید قبلاً در حدود 600 الی 700 درجه سانتیگراد گرم شده باشد و هنگام جوش این حرارت حفظ شود از نظر ترکیبات خاصی که در روپوش وجود دارد با الکترود آسیب دیده نباید جوش داد.
الکترودهای روکش سخت و مقاوم در برابر فرسودگی
رنگ شناسائی : انتها - سبز با خال سفید
الکترود روپوش کلفت اوستنیتی همراه با کرم - نیکل - و مانگانز برای جوشکاری اتصالات عالی و ترک نخور- فولادهای بد جوش یا فولاد ریختگی .جوش روکشی ریل های تراموای سوزن خط آهن - زنجیرهای حرکت تراکتورهای زنجیری و امثال آن - قشر لائی پر مقاومت در روکشهای سخت مخصوصاً قسمتهای فرسوده شونده در فولاد سخت کرم دار مخصوص فولادهای ساده و آلیاژدار با استحکام زیاد- فولادهای احیا شده فولادهای زنگ نزن کرم دار فولادهای مقاوم در پوسته شدن - فولادهای سخت منگنز و فولادهای معمولی.
دارای گواهی از خط آهن آلمان فدرال برای روکشی و جوش دادن فولاد سخت منگنز آما 1090 با قوس آرام ذوب می شود در حال عادی پس از جوشکاری جنس جوش نرم و پر مقاومت است ومی تواند با عملیات سخت کننده سرد تا 400 برینل سخت گردد. جنس جوش به مقدار زیادی زنگ نزن و مقاوم در الکتروشیمی است. تا 800 درجه سانتیگراد سخت است و پوسته نمی کند.
الکترودهای مقاوم در برابر حرارت برای ساختمان تاسیسات نفتی و شیمیائی آماجی 1248
رنگ شناسی : انتها - سفید با خال آبی الکترودی است با روپوش قلیائی و با 5/0% کرم و 5/0% مولیبدن مناسب برای کار به روی فولادهای مقاوم در برابر حرارتهای زیاد و عملیات پر فشار مانند ساختمانهای مراکز جدید تاسیسات نفتی و شیمیائی.
دارای گواهی از کارخانه شل هندی. این الکترود جریان آرام و روان دارد سرباره آن آسان پاک می شود و در تمام وضعیت به آسانی کار می کند. درز آن تمیز و خوش منظره است. برای رسیدن به یک جوش بی نقص نباید الکترود را نوسان داد و همچنین باید حتی المقدور طول قوس را کوتاه نگهداشت. فقط باید الکترودهای خشک مصرف کرد. در صورت مرطوب شدن الکترودها باید آنها را دو ساعت در حرارت 150 درجه سانتیگراد خشک کرد و سپس به مصرف رساند.
پیش گرم کردن قطعه کار از 200 تا 300 درجه سانتیگراد و گرم کردن آن برای رفع تنش از 720 تا 750 درجه سانتیگراد توصیه می شود.
رنگ شناسائی : انتها - سفید با خال سفید استاندارد : آلمانی KB^IS
الکترود قلیائی با روپوش کلفت برای جوشکاری فولادهائی که حداکثر تا 550 درجه سانتیگراد را به طور قائم تحمل می نمایند مانند دیگها- مخزن و لوله ها و فولادهای ریخته گری مخصوص جوشکاری روی فولادهای 17Mn4,19Mn5,15Mo3,HIV و فولاد ریخته گری Gs22Mo4 و فولادهای دانه ریز با مقاومت 50 تا 60 کیلوگرم بر میلی متر مربع آزمایش شده از طرف اتحادیه مراقبتهای فنی آلمان- دفتر آمریکائی و لویدژرمن.
این الکترود دارای قوس آرام و ثابت است. پاشیدن آن بسیار کم می باشد. سرباره در قطعات متوسط به آسانی پاک می شود. منظره گرده جوش تمیز است. اندازه های تا 25/3 میلیمتری آن مخصوص لایه ریز در حالات اجباری درست شده است. این الکترود به طریقه مخصوصی با دو روپوش تهیه گردیده و در تمام حالات به استثنای از بالا به پایین قابل جوشکاری است. (فقط الکترودهای خشک را مصرف نمائید.)
الکترودهای مخصوص جوشکاری سربالا
استاندارد آما 1/322 ن ج رنگ شناسائی : ندارد الکترودی است برای جوشکاری در تمام حالات مخصوصاً عمودی سربالا, دارای قابلیت پل زنی خوب, با این الکترود می توان ورقهای نازک را هم بخوبی ورقهای ضخیم جوش داد. درز جوش ریز فلس بوده و بسیار تمیز است. گرده جوش کمی برجسته و بدون اثر سوختگی است. برای جوشکاری تعمیراتی و جوشکاری نوسازی در اطاق کامیون- قطعات اتومبیل - مخازن و ساختمانهای فولادی و ورقهای نازک مناسب است. برای جوشکاری همیشه طول قوس کوتاه انتخاب کنید. در جوشکاری بالا سر قطر کوچکتری انتخاب نمائید. استاندارد آما 1/421 م.ج رنگ شناسائی انتها : زرد با خال قرمز استاندارد : آمریکائی E 6013 الکترود با روپوش متوسط تیتانی برای جوش اتصالی در ساختمانهای فولادی ماشین سازی- واگن سازی- دیگ و مخزن سازی - کشتی سازی - درزهای لب به لب و گلوئی روی فولادهای ساده st33 , st34 , st33 , st37 , st43 , st52 و فولادهای لوله سازی 35 st , st35/4 , st35/8 , st45 , st45/4 , st45/8 , st55 , st55/4 و فولاد دیگ سازی HIII, HII, HI و فولاد کشتی سازی A, B,C و فولادهای طبق دین 1623 و فولاد رخته گری. دارای گواهی از خط آهن آلمان فدرال تا 52 st - لویدز ژرمن - آزمایش ده از طرف اتحادیه مراقبتهای فنی آلمان. این الکترود به آسانی روشن می شود.پاشیدن کم دارد- در همه حالات جوش می دهد و سرباره آن به آسانی جدا می گردد
|
خصوصيات کاری الکترودها :
مواد تشکیل دهنده روپوش الکترود نه تنها خواص فیزیکی و شیمیایی جوش را تعیین می کند . بلکه خصوصیات کاری الکترود را نیز روشن می سازد . استفاده از الکترودهای مختلف نیاز به فنون مختلفی دارد بنابراین این الکترودها را می توان مطابق خصوصیات کاری و شرایط اتصالات جوش شونده به عنوان پر کن، پی گیر سریع و شکل گیر سریع طبقه بندی نمود
الکترود پر کن سريع :الکترود پرکن سریع سرعت جوشکاری بالایی دارد و نقطه مقابل الکترود شکل گیر سریع (الکترود با انجماد سریع) می باشد گروه الکترود پر کن سریع شامل الکترودهای روپوش دار ضخیم ،پودر آهنی می باشند . که بطور گسترده ای برای جوش های گلوئی و شیاری عمیق مورد استفاده قرا می گیرند . الکترود پر کن سریع به طور ویژه ای برای جوشکاری سریع در حالت تخت طراحی شده است . سرعت جوشکاری آن زیاد پاک کردن سرباره آن آسان است . بریدگی کناره کمی دارد و قوس آن نرم و نفوذ آن کم است . یعنی به مقدار کمی فلز مینا و فلز جوش را مخلوط می نماید . ظاهر جوش خیلی صاف است . رویه تخت تا قدری محدب دارد و پاشیدگی آن کم است . بعضی از این الکترود ها برای جوشکاری حالت غیر عادی تدارک شده اند که خصوصیات منجمد شوندگی آنها سریع تر است مثل الکترود Exx14 . الکترود های Exx24 وExx27 عموما برای جوشکاری گلوئی های تخت و شیاری بکار برده می شوند
الکتروده پی گير سريع :این گروه از الکترودها به عنوان الکترودهای پر کن - زودگیرنیز معروف هستند .آنها خصوصیات ترکیبی پرکنی سریع و شکل گیری سریع را دارا می باشند . در انجام جوشهای لب رولب یا جوشهای ورق نازک فلزی برای تشکیل جوش ، فلز اضافی کمی لازم است . اقتصاد ترین را جوشکاری این نوع اتصال حرکت سریع می باشد به علت آن که بدنبال حرکت قوس ، لازم است هرچه سریعتر چاله تشکیل شود . این نوع الکترودها به الکترودپی گیر سریع معروف هستند . این الکترود قوس نسبتا قوی و نفوذ متوسط دارد . این الکترود همراه با شدت جریان کمتر و ورودی حرارت کمتر ، مساله سوختگی درونی را کاهش می دهد . عموما الکترودهای پی گیر سریع به عنوان الکترودهای قطبیت مستقیم معروف هستند ولی می توانند با جریان متناوب نیز کار کنند . این الکترودها سرباره کاملی دارند و مهره های جوش فلس های صاف دارد . این نوع الکترود ها در کارگاه های تولیدی مصارف عمومی داشته و برای کار تعمیر نیز به طور گسترده استفاده می شوند .در کارگاههای که با ورق نازک سروکار دارند از الکترود پی گیر سریع برای جوشکاری عمومی به صورت سرازیر استفاده می کنند
مثال : این الکترود ها برای جوشکاری با جریان مسقیم Exx12 و برای جوشکاری با جریان متناوب Exx13
الکترود شکل گير سريع : الکترودهای شکل گیر سریع یا الکترود با انجماد سریع جوشی تولید می کند که بسرعت منجمد می شود و شکل می گیرد . این نوع موضوع برای جوشکاری در حالتهای عمودی و سقفی حائز اهمیت است و از ریزش فلز مذاب جلوگیری می شود. الکترودهای شکل گیر سریع قوس قوی و نفوذ عمیق دارند و به الکترود های با قطبیت معکوس معرروفند گرچه بعضی از آنها با جریان متناوب هم کار می کنند . سرباره این الکترود کم است و مهره های تخت تولید می کنند .
با چند استثنا این الکترود ها جوشکاری عکسی (کنترل کیفیت جوش با پرتونگاری )تولید می کنند . و در کارهای کدی لوله و مخزن تحت فشار مورد استفاده قرار می گیرند . این الکترود ها در ساخت و تعمیر برای جوشکاری در همه حالتها به طور گسترده ای به کار برده می شود .
الکترود مرکب : بعضی از اتصالات خصوصیات الکترود ها ی پر کن سریع و شکل گیر سریع را جا لازم دارند بهترین الکترود های شکل گیر سریع یا الکترودهای با ا نجماد سریع الکترودهای Exx10 و Exx11 هستند . الکترود پودر آهنی و مناسب برای همه حالتها که خصوصیات پر کنی سریع و ا نجماد سریع را با هم دارد آنرا الکترود Exx14 می باشند . الکترود Exx14 حالت پر کنی سریع دارد . نه به اندازه Exx10 انجماد سریع دارد بلکه ترکیبی بین این دو می باشد و از این رو الکترود Exx14 الکترود مرکب گفته می شود .
الکترود کم هيدروژن : روپوش این الکترودها کم هیدروژن یا عملا بی هیدروژن هستند . الکترودهای گم هیدروژن جوشهای بدون ترک ریز و زیر مهره ای تولید می کنند و قابلیت نرمی استثنا ئی دارند .
در جوشهای فولادهای گوگرد دار تخلخل ایجاد ننموده و جوشها از نظر پرتو نگاری دارای کیفیت مطلوبی هستند . به دلیل آنکه استفاده از الکترود کم هیدروژن نیاز به گرمایش را کا هش مید هد مصرف عمده آن در جوشکاری فولادهای سخت جوش و فولادهای آ لیاژی با مقاومت کششی بالا می باشد . E7028 E 7018 E7016 E7015 به بعنوان مثال: این الکترودها عبارتند از: ٍExx28 و Exx18
الکترود پود آ هنی : پودر آ هن در روپوش بسیاری از الکترودها اضا فه می شود . پودر آ هن در حرارت شدید قوس تبدیل به مذاب شده و به فلز جوش استفاده میشود . وقتی پودر آ هن در مقادیر نسبتا زیاد 30 درصد بیشتر به روپوش اضافه میشود سرعت جوشکاری بطور قابل ملاحظه ای افزایش می یابد و پاک کردن سرباره آسان تر می گردد . ضاهر جوش خیلی صاف است . مثال : برای الکترودهای پودر آهنی می توان الکترودهای ٍE7027 , E7028 , E7024 را نام برد
|
زاويه دادن به الکترود در وضعيت های مختلف جوشکاری Electrode Angle
علاوه بر سه حرکت اشاره شده در بالا جوشکار باید الکترود را با زاویه ، معین و مشخص نسبت به سطح کار و امتداد جوش نگه دارد . زاویه بین الکترود با خط عمود بر جوش در صفحه طولی را زاویه راهنما Lead angle و زاویه الکترود با خط عمود برجوش در صفحه عرضی را زاویه کار می گویند . وضعیت صحیح الکترود باعث کاهش ذرات حبس شده سرباره در جوش و تقلیل زیر جوش under cUT می شود . در میانه کار معمولا جوشکار باید برای قرار دادن الکترود های جدید قوس را چندین بار مرتبا قطع کند . اگر قوس در نتیجه عقب کشیدن آنی الکترود قطع شود حفره ای کاسه شکل بدون اینکه از فلز مذاب کافی پر شود ایجاد می گردد که شبیه دهانه آتش فشان می باشد و احتمال ایجاد عیوب در این ناحیه زیاد است برای جولوگیری از وقوع این دهانه بر روی باند جوش در خاتمه هر الکترود بهتر است الکترود را به آهستگی به عقب در سر تا سر گرده جوش کشیده و همزمان طول قوس را افزایش داد . قبل از شروع الکترود بعدی باید این ناحیه را تمیز کرد تا از محبوس شدن سرباره اجتناب شود . قوس در الکترود بعدی پیشاپیش دهانه شروع و به عقب برگشت داده تا انتهای قبلی باند جوش را در بر گیرد . نقطه تعویض الکترود یک منبع جدی برای تجمع سرباره و حباب گاز و فقدان ذوب کامل جوش است . این قسمت از عملیات جوشکاری احتیاج به مهارت زیاد دارد تا بتوان جوش با کیفیت خوب تولید نمود . همانطور که قبلا اشاره شد انتهای الکترود باید به اندازۀ کافی به کار نزدیک باشد تا قطرات مذاب مستقیم از الکترود به حوضچه جوش منتقل شود . طول قوس فاصله بین انتهای الکترود و حوضچه جوش است که تا حدودی تابع نوع پوشش الکترود و شرایط کار می باشد . به طور کلی طول قوس نباید از قطر هسته الکترود بیشتر باشد و جوشکار باید با مهرت و تجربه ای که دارد آنرا کنترل کند . طول قوس کنترل کننده ولتاژ قوس بوده و بر سرعت پیشرفت جوش و راندمان آن تاثیر می گذارد . با قوس کوتاه شدت جریان افزایش یافته و در نتیجه نرخ رسوب زیاد می شود . در حالیکه قوس بلند احتمال اکسیده و نیتره شدن مذاب را بیشتر کرده و مقداری حرارت قوس تلف شده و تولید جرقه به مراتب بیشتر می شود . اگر لازم است که چندین پاس و لایه جوش کناره و یا روی هم رسوب داده شود باید توجه داشت که سرباره از روی لایه های قبلی کاملا پاک شود در مواردی که پاس ها کنار یکدیگر قرار می گیرند به منظور حذف زاویه تندبین دو پاس و کاهش موضع تمرکز تنش حاصل از آن الزامی است
حرکت الکترود :
پس از شروع قوس الکتریکی ، جوشکاری باید قوس الکتریکی را به داخل محل اتصال جهت دهد تا فلز جوش در محل مورد نظر رسوب داده شود . برای اینکار جوشکار باید سه حرکت را همزمان بطور یکنواخت و قابل کنترل انجام دهد که عبارت است از :
الف: تثبیت فاصله نوک الکترود با سطح مذاب حوضچه جوش یا انطباق همزمان ذوب الکترود و حرکت آن سوی و سمت جوش
ب: حرکت الکترود و قوس در سر تا سر مسیر جوش که در اصل سرعت پیشرفت جوشکاری است
ج: در صورت لزوم حرکت های زیگزاکی یا موجی متناسب با وضعیت جوش ، تا نیروی قوس فلز مذاب را در محل مورد لزوم هدایت داده نگه دارد و سر باره را نیز به اطراف جارو کند .لازم به تذکر است که این حرکت ها باید به طریقی انجام شود تا باعث حبس شدن ذرات سرباره در جوش یا وارد شدن هوای اتمسفر به محفظه قوس نشود .
نرخ يا ميزان ذوب الکترود : Melting rate
طول الکترود ذوب شده در دقیقه را نرخ ذوب الکترود می نامند . نرخ ذوب الکترود به عوامل مختلفی بستگی دارد و در شرایط مشابه (از نظر اندازه و شدت جریان ) در موتورهای زنراتور بیشتر از ترانسفورماتورهای یکسوکننده و در ترانسفورماتورهای یکسو کننده بیشتر از ترانسفورماتورهای AC است . برای منبع با قدرت معین نرخ ذوب با ازدیاد شدت جریان افزایش می یابد . ولی شدت افزایش در الکترودهای ضخیم تر کمتر از الکترودهای باریک است . باید توجه داشت که در شدت جریان های خیلی زیاد به علت وزش قوس و جرقه و حرارت مقاومتی زیاد در الکترود ، نرخ ذوب دوباره اندکی کاهش می یابد .
انتقال فلز از الکترود به حوضچه مذاب Metal transfer - Droplet transfer
انتقال فلز مذاب از الکترود مصرفی به طرف حوضچه جوش اثر مهمی بر روی استفاده فرآیند جوشکاری و قابلیت آنها برای اتصال در وضعیت های مختلف دارد . نحوه انتقال قطرات مذاب ممکن است بر روی میزان عمق نفوذ پایداری حوضچه جوش و مقدار ترشح و جرقه نیز تاثیر داشته باشد .انواع مکانیزههای انتقال فلز از الکترود به حوضچه جوشی در شکل زیر نشان داده می شود .
شكل (a): Spray transfer
سكل (b): Globular transfer شكل (c): Short circuit transfer
انتقال ثقلی يا کروی : Globular Transfer - Gravitation Transfer
در این مکانیزم قطر قطرات ذوب شده از الکترود مساوی یا بزرگتر از قطر الکترود است
.
جوشکاری با الکترود از نوع کم هیدروزن جوشکاری قوس با گاز Co2 با جریان بالا و جوشکاری MIG با جریان پایین این نوع انتقال فلز را دارا می باشد . در این مکانیزه جرقه یا ترشح براحتی بوقوع می پیوندد
انتقال مدار بسته يا پلی : Short Circuit Transfer در این مکانیزم قطرات ذوب شده در انتهای الکترود با حوضچه جوش به صورت پلی قرار می گیرند . جوشکاری قوس با گاز محافظ با جریان پایین این نوع مکانیزم انتقال را دارا می باشد .این نوع جوشکاری برای جوشکاری ورقهای نازک با عمق نفوذ کم و در جاهایی که جوشکاری یکطرفه بوده و بستر جوش با کیفیت مناسب در جهت دیگر مد نظر می باشد مناسب است .
انتقال اسپري يا انتقال ريزش شديد :Spray transfer
در اين مكانيزم قطرات با قطر كوچكتر از قطر الكترود از ميان ستون قوس به سمت حوضچه پرتاب مي شوند . جوشكاري MIG با جريان نسبتا بالا و جوشكاري با الكترود ا زنوع اكسيد تيتانيم بالا اين نوع انتقال را دارا مي باشد . قوس در اين حالت معمولا پايدار بوده و جرقه كمي توليد مي كند .
نيروهايي كه در انتقال فلز از الكترود به حوضچه جوش نقش دارند عبارتند از:
الف : كشش سطحي
ب : شتاب ثقل (وزن )
ج : نيروي الكترومغناطيس
د : هيدرو ديناميك در اثر جريان و جنبش گازها
معمولا نوع انتقال به تركيب الكترود و فلاكس ، قطر الكترود ،قطب الكتريكي ،گاز محافظ و عوامل ديگر بستگي دارد. براي ثبت و مشاهده و نحوه انتقال فلز از الكترود به حوضچه جوش از دوربين هاي فيلمبرداري با سرعت بالا (10000 فيلم در ثانيه ) استفاده مي شود .
الکترود
جنس هسته الکترود :
بطور کلی متریال مورد استفاده در ساخت هسته الکترود را بدو گروه عمده تقسیم می کنند .
الف:گروه آهنی : نظیر فولاد
ب:گروه غیر آهنی : نظیر مس ، آلومینیوم
لازم به توضیح است که در گروه آهنی هم از فولاد های ساده کم کربن بهره می گیرند و هم از فولادهای آلیازی .
مثلا برای جوشکاری فولاد های ضد زنگ از الکترودهایی استفاده می کنند . که جنس هسته آن از فولاد پر آلیاژ باشد . این الکترودها در بازار به الکترودهای استیل معروفند .
مواد سازنده پوشش الکترود :
الف:سلولز : ترکیب شیمیایی غیر کامل از خمیر چوب که تولید کننده گاز COو H2 می باشد .
ب: اکسید تیتانیوم که نام دیگر آن روتایل است . (Tio2)
ج: اکسید آلومینیوم که نام دیگر آن آلومنیی است . (Al2o3)
د: اکسید آهن .
ه: کربنات آهن - کربنات کلسیم - کربنات منیزیم .
و: فلدسپات (که ترکیبی از آلومنینیم سیلسکات است ) .
ز: بعضی از سیلسکات ها که سرباره ساز هستند .
ح: بعضی از سیلسکات ها که نقش چسب را دارند مثل سیلیکات سدیم و سیلیکات پتاسیم .
ط: فرو آلیاژ ها مثل فرمنگنز و فرو سیلیس .
ی: پودر آهن از 5 تا 50 در صد .
وظایف پوشش الکترود :
الف : فضای گازی و سرباره محافظ را بوجود می آورد و حوضچه مذاب را از تماس با اتمسفر محافظت می کند .
ب: پایدار کننده قوس می باشد .
ج: وظیفه افزون برخی عناصر آلیازی را به حوضچه جوش بر عهده دارد .
د : به کمک ویسکوزیته ای که دارد شکل گردۀ جوش را منظم و قانونمند می کند .
ه: پوشش از سریع سرد شدن جوش جلوگیری کرده و رسیدن به خواص مکانیکی مطلوب را ممکن می سازد .
و : کاهش دهنده پاشش فلز جوش به اطراف بوده و عمل رسوب فلز را به حوضچه تسهیل می بخشد .
ز: تشکیل سرباره داده و لزا واکنش های سرباره و فلز مذاب را خواهیم داشت که این امر در تصفیه نا خالصی ها از حوضچه مذاب کمک خواهد کرد .
ح: بر روی می زان نفوذ قوس تاثیر خواهد داشت
همانطور که می توان انتظار داشت الکترودی ساخته نشده است که کلیه خواسته ها را در تمام شرایط پاسخگو باشد بنابر این انواع گوناگون الکترود تولید می شود که هر نوع آن مناسب برای درخواست های خاصی است .عناصر مختلفی در پوشش الکترود بکار گرفته می شود که در هنگام ساخت الکترود پس از انتخاب مواد پوشش آنها را مخلوط کرده و با اضافه کردن مواد چسبنده (چسب شیشه) بصورت خمیر در می آورند . سپس این خمیر را از طریق اکسترود (Extrude) بر روی میله فولادی بصورت یکنواخت پوشش می دهند و پس از خشک کردن در کوره پخته می شوند .
طبقه بندی پوشش های الکترود ها :
این طبقه بندی بر اساس استاندارد جهانی ISO ارائه شده است . بر اساس پوشش ها را به شش کلاس تقسیم می کنند .
کلاس اول یا سلولزی : پوشش این نوع الکترودها از مقدار زیادی سلولز تشکیل شده است که در اثر سوختن آن مقداری زیاد هیدروزن و اکسید کربن به وجود می آید که قوس و حوضچه جوش را از اتمسفر محافظت می نماید . حضور این گازها در قوس الکتریکی با قدرت (یونیزه شدن) بالا ایجاد ولتاژ بالای قوس کرده و در نتیجه انرزی تولید شده بالا بوده و موجب نرخ بالای سوختن Burn - off rate و عمق نفوذ جوش خوب می شود . قسمتس از ترکیبات سلولز در اثر حرارت مقاومتی تولید شده در هسته الکترود حین جوشکاری تمایل به تجربه دارد . گرم شدن الکترود هم چنین یک (افت)کوچک ولتاز قوس شده که احیانا می تواند ترکیب شیمیایی جوش راتغییر دهد . همانطور که می توان انتظار داشت چون بیشتر مواد کربنی و سوختنی در پوشش این نوع الکترودها است . در پایان سرباره کمی بر روی جوش باقی می ماند ولی قوس حاصل شده به علت (جت پلاسمای ) قوس این مکان را به الکترود می دهد تا در وضعیت های مختلف استفاده می شود . نبودن عناصر پایدار مننده قوس در پوشش موجب آن می شود تا این الکترود را با جریان الکتریکی یکنواخت و قطب مثبت بکار برند .
کلاس دوم و سوم یا رتیلی: اکسید تیتانیوم به صورت طبیعی آن (رتیل) پوشش اصلی این دو نوع الکترودها است . وجود مقدار زیادی مواد یونیزه کننده استفادده از الکترود را آسان می سازد . در نوع دوم به علت وجود ترکیبات بازی اضافه شده روان تر بوده و برای وضعیت های دیگر هم مناسب می باشد . یک نفوذ متوسط همراه با قوس ملایم و آرامیکی از مشخصات این نوع الکترود می باشد . به علت وجود رتیل و عناصر یونیزه کننده در پوشش الکترود می توان این گروه الکترودها را با جریان متناوب هم بکار برد .
کلاس چهارم یا اسیدی : پوشش این نوع الکترودها شامل اکسید ها و کربناتهای منگنز و آهن و مقداری سیلسیم می باشد . این پوشش تولید یک سرباره حجیم و روان کرده که نتیجه آن جوش با ظاهر بسیار صاف و تمیز می باشد .سر باره براحتی از روی جوش جدا می شود . هم چنین از وقوع ذرات سرباره محبوسشده در جوش چند (پاسه)می کاهد . با این الکترود می توان از جریان یکنواخت و متناوب استفاده کرد .
کلاس پنجم یا اکسیدی : اکسید آهن به مقدار زیاد در پوشش آن است و به علت سرباره سنگین مقدار نفوذ جوش کم بوده اما جوش حاصل پخ و صاف می باشد ولی دارای استحکام کمتری نسبت به جوش حاصل از الکترودهای دیگر است .
کلاس ششم یا بازی : احتمالا مهمترین نوع الکترود از نظر متالوژیکی است . پوشش الکترود شامل مقدار قابل ملاحضه ای کربنات کلسیم و فلورید آهک و فلوراسپار می باشد . به علت می زان رطوبت کم در پوشش الکترود جوش حاصل دارای می نیمم مقدار هیدروزن شده است . همه الکترودهای هیدروزن پائین لزوما از این نوع نیست . به علت تولید فلز جوش با هیدروزن کم ، این نوع الکترود برای جوشکاری فولادی کم آلیاژی که در مقابل (ترک برداشتن) منطقه مجاور جوش حساس هستند .بسیار مناسب می باشد همچنین جوش حاصل مقاومت خوبی در برار (ترک گرم) دارد.
|
|
|
|
|
چنانچه بخواهیم دو قطعه فلز را به هم جوش داده و یا شکافی را بوسیله عمل جوش کاری پر کنیم از فلز دیگری استفاده می شود که انرا الکترود یا سیم جوش می نامند.
الکترود در جوش کاری با قوس الکتریکی عبارت است از یک میله ی فلزی که اطراف انرا پوششی از ترکیبات شیمیایی بخصوصی متناسب با نوع مصرف ان احاطه کرده است .انواع پوششها بسته به نوع فلز مورد جوش کاری و نیز مراحل مختلف جوش کاری متفاوت می باشند و برای جوش کاری ضروری است که انها را شناخته وموارد استفاده صحیح انها را نیز از هم دیگر تمیز دهد .
طبقه بندی الکترودها
طبقه بندی الکترودها از لحاظ جنس فلز :
به طور کلی الکترودها از لحاظ جنس فلز به پنج گروه تقسیم می شوند :
1-الکترودهای اهنی hild steel
2-الکترودهای چدنی cast iron
3-الکترودهای الیاژهای فولادی special alloy steel
4-الکترودهای فولادهای پرکربن high carbon steel
5-الکترودهای غیر اهنی none ferrouse
از انجایی که اکثر جوشکاری ها روی اهن و الیاژهای ان انجام می گیرد لذا الکترودهایی که برای اهن مصرف می شوند نسبت به انواع دیگر زیادترند . الیازهای فولاد در جوشکاری فولادهی مختلف و الکترودهای غیر اهنی برای جوشکاری فلزات مختلف از قبیل :الومینیم - مس – برنز –برنج و ... مورد مصرف دارند .برای جوشکاری دو قطعه فلز به یکدیگر معمولا از الکترودهایی استفاده می شود که جنس انها با فلز مبنا یکی باشد .
الکترودها نه تنها نسبت به فلزات مختلف متفاوتند بلکه نسبت به نوع جریان وحالتهای گوناگون جوشکاری و مقدار نفوذ جوش نیز انواع مختلف دارند . چنانچه الکترود ها نسبت به نوع کار صحیح انتخاب نشوند ماکزیمم مقاومت و استقامت را در برا بر فساد تدریجی نداشته و در بعضی موارد باعث شکنندگی فلز نیز خواهند شد .البته استثناهایی نیز وجود دارد که برای انها الکترودها ی ویژه ای تهیه شده است .مانند اتصال قطعات برنج و چدن یا برنج و اهن به یکدیگر .
تقسیم بندی الکترودهای فلزی از نظر نوع پوشش :
بطور کلی الکترودهای فلزی به دو دسته تقسیم می شود:
الکترود های پوشش دار والکترود های بدون پوشش.
الکترود های پوشش دار:
پوشش این نوع الکترود ها از ترکیبات شیمیایی متنوعی است که مقداری از انها معین ومقداری دیگر نا مشخص می باشند .علت مشخص نبودن بعضی ترکیبات الکترد ها به دلیل ارزش اقتصادی انها است که کارخانه سازنده فرمول کامل الکترود های خود را محرمانه نگداری می کند. مهمترین ترکیبات شیمیایی پوشش این نوع الکترودها عبارتند از : سولفورید – فرومنگنز – دی اکسید تیتانیم- کربنات کلسیم- سیلیکات های مختلف- و غیره .
برای چسبندگی انها به سیم جوش از سیلیکات سدیم استفاده می کنند و تمام ترکیبات شیمیایی پوشش الکترودها هر کدام به تنهایی نقش مهمی را در جوشکاری ایفا می کنند که مهمترین انها محافظت ناحیه جوش از اکسیداسیون ، یکنواخت و پایدار کردن قوس الکتریکی و ایجاد ترکیبات معین در ناحیه جوش می باشند. پوشش الکترودها از نظر کلی به دو گروه اصلی تقسیم می شوند :
1- پوشش های پایدار کننده یا پوشش های نازک .
2-پوشش های کیفی یا پوشش های ضخیم .
پوشش های پایدار کننده :
عناصری که این پوشش ها را تشکیل می دهند فضای قوس الکتریکی را یونیزه نموده و جوشکاری با جریان متناوب را اسنتر می نماید. بهترین و مطمئن ترین عنصر برای این کار پتاسیم می باشد که در سنگهای معدنی طبیعی ( گرافیت فلدسپات ) و بصورت شیمیایی (کرومات پتاسیم و دی کرمات پتاسیم ، پتاس و شوره ) یافت می شود.
به دلیل نازک بودن این پوشش ها امکان نفوذ اکسیژن و ازت هوا به ناحیه مذاب جوش همیشه وجود داشته و باعث ترد شدن نسبی جوش می گردند لذا استفاده انها در جوشکای های غیر حساس بلا مانع خواهد بود .
پوشش های کیفی :این پوشش ها گاز و سرباره برای محا فظت فلز از نفوذ اکسیژن و ازت هوا تشکیل داده و نیز آلیاژهای مناسب را در ناحیه مذاب وارد می کنند در نتیجه استفاده از این نوع الکترودها خواص مکانیکی پیوند جوش معمولا بالا تر از خواص فلز مبنا می گردد .
این پوشش ها دارای خواص زیر هستند :
1_ هنگام ذوب ،سرباره و گازهای محافظ تولید می کنند .
2_ قوس الکتریکی پایدار وپیوسته می گردد .
3_ سرباره و تفاله جوش دارای خاصیت احیا کنندگی می باشند
4- تفاله جوش دارای خاصیت انقباضی بیشتری نسبت به فلز مبنا بوده ودرنتیجه به راحتی از روی گرده جوش جدا می شوند
5_ در جوشکاری های عمودی و بالای سر، تفاله به سرعت منجمد می شود و در نتیجه از سقوط مواد مذاب بر اثر جاذبه زمین جلو گیری می کنند.
تقسيم بندي اكترودهاي پوششدار بر اساس تركيبات شيميايي پوشش ها :
1- الكترودهاي اسيدي يا گرم:
الكترودهاي اسيدي الكترودهايي هستند كه موارد استعمالشان در درزهاي بسته،مانند اتصالات سپري مي باشند. با اينكه در زمره الكترودهاي مرغوب به شمار مي آيند لكن اكثر جوشكارها از كار كردن با اين الكترودها امتناع مي ورزند زيرا شكل ظاهري جوش يكنواخت نبوده و در موقع كار جرقه هايي به اطراف پراكنده مي كند. علت اينكه نمي توان از آنها در درزهاي باز استفاده نمود،اولا" نسبت به الكترودها ي هم قطر خود احتياج به شدت جريان زيادي داشته ثانيأ قطرات مذاب آنها ريزند و ريز بودن قطرات مذاب باعث سوزاندن لبه هاي قطعه كار مي گردد. سرباره حاصل از جوشكاري اين الكترودها خاصيت اسيدي دارند. مقاومت كششي جوش حاصل از اين الكترودها كمتر از الكترودهاي روتايلي بوده اما افزايش طول و استحكام ضربه اي آنها بيشتر است.
2- الكترودهاي بازي يا قليايي (آهكي يا سرد):
اين نوع الكترودها با اينكه محاسن زيادي از نظر جوشكاري دارند. چنانچه بطور صحيح بكار برده نشوند گرده جوش معايب زيادي پيدا كرده و از جمله تمامي آن متخلخل و در انتهاي آن حفره بزرگي ايجاد مي گردد. با توجه به نفوذ خيلي خوب آنها بيشتر در پاسهاي اول جوشكاري مورد استفاده قرار مي گيرند در جوشكاري به حالت عمودي سرعت جوش آنها بيشتر از ساير الكترودها است فلز جوش حاصل از اين نوع الكترودها هيدروژن كمتري داشته و معمولأ در درجات حرارت پايين از استحكام خوبي برخوردار است در مقايسه با ساير الكترودها احتمال ترك خوردن گرم يا سرد با الكترودهاي آهكي كمتر است. از اين نظر در جوشكاري فولادهاي ساختماني پر منگنز، مخازن تحت فشار و امثال آنها نسبت به ساير الكترودها ارجعيت دارد.
3-الكترودهاي دي اكسيد تيتانيم يا روتيلي:
اين نوع الكترودها كه مقدار قابل توجهي دي اكسيد تيتانيم در تركيبات پوششي خوردارند الكترودهايي هستند كه شروع جوش و مصرف آساني داشته و براي حالتهاي مختلف جوشكاري بسيار مناسب اند. گرده جوش اين الكترودها داراي خاتمه ظريف بوده و افت فلز از نظر پاشيدگي كم مي باشد. نفوذ اين الكترودها متوسط و قوس الكتريكي آنها آرام است. برخي از اين الكترودهاي براي جوشكاري عمودي از بالا به پايين بكار برده ميشوند.
4-الكترودهاي سلولزي:
اين نوع الكترودها داراي نفوذ بسيار زياد بوده و براي جوشكاري حالات مختلف مناسب مي باشند. سرباره آنها نازك بوده و به راحتي از روي گرده جوش كنده ميشوند. جوش حاصل از اين نوع الكترودها داراي خواص مكانيكي خوبي بوده و از نظر آزمايش راديوگرافي نتيجه خوبي دارند. ماده اصلي تشكيل دهنده پوشش آنها سلولز است كه موقع جوشكاري توليد گاز محافظ ميكند. اين الكترودها داراي دود زياد بوده و سطح جوش ناهموار و خشن است.
5-الكترودهاي اكسيدي:
پوشش اين نوع الكترودها بيشتر از اكسيد آهن و اكسيد منگنز تشكيل ميشود. تفاله جوش براحتي از روي گرده جوش كنده ميشود. از آنجايي كه فلز جوش اين الكترودها سيال است لذا بيشتر براي اتصالات گوشه اي و درزهاي بسته مورد مصرف دارند. اين الكترودها در جاهايي كه ظاهر جوش بر كيفيت آن ارجعيت دارند مورد استفاده قرار مي گيرند.
6-الكترودهاي مركب:
علاوه بر پوشش هاي مذكور از مخلوط كردن مواد مختلف نيز پوشش هاي مركبي با خواص گوناگون حصل ميشود. مانند پوشش هاي اسيدي- روتايلي يا روتايلي- قليايي كه براي فولادهاي با مقاومت زياد مناسب ترين الكترود مي باشند.
تقسيم بندي الكترودها از نظر ضخامت پوشش:
چنانچه قطر پوشش الكترود را با D و قطر ميله الكترود را با d نمايش دهيم تقسيم بندي هاي زير از نظر پوشش معمول است:
1-پوشش نازك
2-پوشش متوسط
3-پوشش ضخيم
4-پوشش خيلي ضخيم
شناسايي الكترودها:
براي سهولت كار و چگونگي اجراي الكترودها بطور كلي الكترودها را بوسيله رنگ يا خال رنگ و يا طلايي كه روي جعبه آنها حك يا نوشته شده است، شناسايي ميكنند.
هدف از ایجاد لکه رنگی روی الکترود چسب شناسایی سریع است .وقتی الکترود در الکترود گیر باشد ،باز هم این لکه به اسانی دیده می شود.
معمولأ هر یک از کشورهای صنعتی روش خاصی را با توجه به مراتب فوق در شناسایی و نحوه استفاده از الکترودهای ود بکار می برند. لذا جهت آشنایی با انواع الکترودهای بعضی از کشورهای صنعتی در زیر نحوه شناسایی برخی از آنها توضیح داده میشود:
شناسایی الکترودها از طریق حروف یا اعداد:
1-طبقه بندی الکترودهای آمریکایی :
انجمن جوشکاران آمریکا که علایم اختصاری الکترودهای آمریکایی را تحت قوانین ویژه ای تهیه و تعیین کرده است و کارخانجات سازنده الکترود نیز عضو انجمن مذکور می باشند روی جعبه الکترودها علامت A.W.S یعنی American Weiding Society را حک کرده اند. همچنین انجمن آزمایش فلزات نیز با انجمن مذکور همکاری داشته و غیر از علایم فوق، علایم دیگری نیز روی جعبه های الکترودها دیده میشود که عبارتند از: A.S.T.M یعنی American Society Testing Materials غیر از علایم فوق علامت دیگری نیز وجود دارد که با هر کدام از آنها روش یا نوع بخصوصی می باشند.مثلا E-6010 که این علامت به شرح زیر رده بندی می گردد:
حرف E یعنی الکترود جوش برق، عدد اول که همیشه یک عدد دو یا سه رقمی می باشد نشان دهنده اتحکام کششی فلز الکترود، عدد دوم که یک عدد یک رقمی است نشان دهنده حالت جوش و بالاخره عدد سوم که باز عددی است یک رقمی صفات مشخصه جوش را معلوم می کند.
عدد دورقمی اول: مثلأ 60 که نشان دهنده استحکام کششی فلز الکترود است باید در عدد 100 ضرب شود تا استحکام کششی جنس الکترود را بر حسب پوند بر اینچ مربع بیان کند در سیستم متریک کافی است عدد 60 را در عدد 7/0 ضرب نمود تا استحکام کششی فلز الکترود بر حسب کیلو گرم بر میلی متر مربع به دست آید.
از آنجایی که ر کشورهای صنعتی اروپایی و در کشور ایران فولادها را براساس استحکام کششی آنها طبقه بندی می کنند در نتیجه چنانچه دو رقم سمت چپ علایم مذکور عدد 60 باشد یعنی اینکه فلز این نوع الکترودها از فولاد ساخته شده است و اگر دو رقم سمت چپ علامت مذکور 70 باشد یعنی جنس الکترود از فولاد می باشد.
عدد دوم :حالت جوش را بیان می کند و در این مرتبه عدد مورد نظر همیشه اعداد 1 و2 و3 می باشند الکترودهایی که عدد دوم آنها رقم 1 باشد می توانند در تماس حالات جوش مورد استفاده قرار گیرند. الکترودهایی که عدد دوم آنها عدد 2 باشد فقط در حالات سطحی و افقی می توان از آنها استفاده کرد و بالاخره اگر عدد دوم آنها 3 باشد یعنی اینکه از این الکترودها فقط در حالت سطحی می توان استفاده کرد.
عدد سوم: خصوصیات ظاهری گرده جوش و روش بکار بردن الکترودها را نشان می دهد و این علامت معمولأ از رقم صفر شروع و به رقم 8 خاتمه می یابد و در نتیجه خصوصیات الکترودها را به شرح زیر بیان میکند:
الف- اگر عدد سوم رقم صفر باشد موارد استعمال الکترودها تنها در ژنراتور با قطب معکوس می باشد. به استثناء الکترودهایی که علایم آنها به اعداد 20 یا 30 ختم میشوند که این دو گروه الکترودها با هر دو قطب جریان مستقیم قابل جوشکاری هستند. نفوذ این الکترودها زیاد، شکل گرده جوش تخت یا مقعر و درجه سختی جوش زیاد است.
تذکر: نمای جوش از لحاظ محدب، مقعر یا تخت بودن تنها در اتصال سپری و زاویه ای مشخص می باشد در غیر این صورت در روی ورق صاف یا اتصالات لب به لب همه الکترودها دارای گرده جوش محدب خواهند بود.
ب- چنانچه علامت آخر عدد 1 باشد یعنی اینکه این الکترودها قابل جوشکاری با جریان مستقیم با قطب معکوس می باشند. شکل ظاهری این جوشها صاف و در بعضی مواقع کمی مقعر و درجه سختی آنها زیاد است. موارد استعمال این نوع الکترودها معمولأ در مواقعی است که قطعه جوش شده نیاز به استقامت زیادی در برابر فشارهای وارده داشته باشد.
ج- چنانچه علامت آخر عدد 2 باشد یعنی اینکه این الکترودها قابل جوشکاری با جریان متناوب و جریان مستقیم با قطب مستقیم می باشند. نفوذ این نوع الکترودها متوسط، سختی جوش کمتر از گروه قبلی بوده و ظاهر جوش محدب و در بعضی مواقع تخت است.
د- چنانچه علامت آخر 3 باشد یعنی اینکه این الکترودها قابل جوشکاری با جریانهای متناوب و مستقیم می باشند. این الکترودها دارای قوس الکتریکی آرام و نفوذ کم هستند شکل گرده جوش آنها معمولأ محدب می باشد.
ه- چنانچه علامت چهارم عدد 3 باشد یعنی اینکه این الکترودها قابل جوشکاری با جریان متناوب و جریان مستقیم می باشند. موارد استعمال این نوع الکترودها در شکافهای عمیق و یا در جاهایی است که نیاز به ساختن چندین گرده جوش روی هم باشد.
و- چنانچه علامت و چهارم عدد 5 باشد نشان دهنده این است که در ترکیبات پوشش این الکترودها هیدروژن کم مصرف شده است. که برای شکافهای باز و پاسهای او مناسب اند. شکل گرده جوش این نوع الکترودها محدب و تنها با جریان مستقیم و قطب معکوس قابل جوشکاری می باشند. درجه سختی جوش در این الکترودها کم و در جوش نفوذ آنها بسیار زیاد و دارای قوس الکتریکی بسیار آرام می باشند.
ز- چنانچه علامت آخر عدد 6 باشد یعنی اینکه صفات مشخصه جوش نظیر گرده قبلی است با این تفاوت که با جریان متناوب قابل جوشکاری می باشند و در بعضی مواقع می توان از قطب معکوس ژنراتور استفاده کرد.
همچنین چنانچه علامت آخر عدد 7و8 باشد نشان دهنده این است که در ساخت این الکترودها پودر آهن بکار رفته است. با این تفاوت که الکترودی که عدد آخر آن 8 است الکترود کم هیدروژنه می باشد و در استفاده از این الکترود باید از جریان متناوب و مستقیم با قطب معکوس استفاده کرد.
علاوه بر این شماره آخر الکترودها نیز مشخص کننده ترکیب شیمیایی الکترودها نیز می باشند که به صورت زیر می توان آنها را طبقه بندی کرد:
0 پوشش پر سلولز و کربنات سدیم
1 پوشش پر سلولز و کربنات پتاسیم
2 پوشش پر تیتان و کربنات سدیم
3 پوشش پر تیتان و کربنات پتاسیم
4 پوشش پر تیتان و پودر آهن
5 پوشش کم هیدروژنه
7 پوشش کم هیدروژنه
8 پوشش کم هیدروژنه و حاوی پودراهن
با توجه به نکات فوق می توان از روی علائم روی جعبه موارد استعمال الکترودهای آمریکایی را مشخص نمود.
2- طبقه بندی الکترودهای انگلیسی:
براساس استاندارد BS-630 انگلیسی کدهای طبقه بندی الکترودها از دو قسمت اجباری و اختیاری تشکیل می گردد.
الف) قسمت اجباری:
قسمت اجباری از قسمتهای زیر تشکیل یافته است:
1-حرف E به معنای الکترود پوشش دار قوس الکتریکی
2- یک عدد دو رقمی نشان دهنده استحکام کششی و تنش تسلیم فلز جوش بر حسب N/mm 2
3- یک عدد دو رقمی بیان کننده مقادیر افزایش طول و مقاومت در برابر ضربه فلز جوش
4- حرف یا حروف مربوط به نوع پوشش الکترود
ب) قسمت اختیاری:
قسمت اختیاری از قسمتهای زیر تشکیل شده است:
1-یک عدد سه رقمی برای راندمان اسمی الکترود
2- یک عدد یک رقمی بیان کننده حالات جوشکاری
3- یک عدد یک رقمی بیان کننده شدت جریان و شرایط ولتاژ توصیه شده
4- حرف H برای الکترودهای با هیدروژن کنترل شده
* چنانچه عدد مذکور 1 باشد یعنی اینکه قابل جوشکاری در تمامی حالات است.
* چنانچه عدد مذکور 2 باشد یعنی تمامی حالات جوشکاری به استثنای حالت عمودی ار بالا به پایین
* چنانچه عدد مذکور 3 باشد یعنی حالت تخت برای جوشهای لب به لب، تخت، افقی و عمودی و برای جوشهای گوشه ای
* چنانچه عدد مذکور 4 باشد یعنی اینکه قابل جوشکاری فقط در حالت تخت
* چنانچه عدد مذکور 5 باشد یعنی حالات تخت، عمودی از بالا به پایین برای جوشهای لب به لب، افقی و عمودی برای جوشهای گوشه ای
* چنانچه عدد مذکور 6 باشد یعنی قابل جوشکاری در هر حالت یا ترکیب حالات مختلف که در بالا طبقه بندی نگردیده است.
در مورد شدت جریان و شرایط ولتاژ باید با توجه به جدول زیر عمل نمود:
برای روشن شدن موارد فوق به مثال کلی زیر اکتفا می شود :
E 51 33 B 160 2 0 H
E الکترود پوشش دار قوس الکتریکی_دستی
51 مقاومت کششی نش تسلیمی بر حسب نیوتن بر میلی متر مربع
33 افزایش طول بر حسب درصد و مقاومت ضربه ای
B روپوش از نوع اهکی
160 راندمان الکترود
2 جوشکاری در تمام حالات به جز عمودی از بالا به پایین
0 جریان مستقیم و قطب توصیه شده به وسیله ی سازنده
H هیدروژن کنترل شده
تذکر:در مورد اعداد دو رقمی مربوط به مقاومت کششی و تنش تسلیمی باید دو عدد مورد نظر را در 10 ضرب نمود تا مقاومت کششی آن بر حسب نیوتن بر میلی متر مربع حاصل شود.
3- طبقه بندی الکترودهای آلمانی:
الکترودهای آلمان براساس برگ فرم شماره 1913 آن کشورDIN 1913 به شرح فوق طبقه بندی می شوند.
حرف مشخص کننده پوشش عدد یک رقمی عدد دو رقمی
دو طبقه بندی فوق حرف E به معنای الکترود پوشش دار عدد دو رقمی اول نشان دهنده مقاومت کششی و تنش تسلیمی فلز الکترود عدد دوم نشان دهنده افزایش طول و مقدار ضربه فلز جوش- عدد سوم نمایشگر حالات جوشکاری حروف آخر بیانگر نوع پوشش شیمیایی الکترود می باشند. در مورد حالات جوشکاری:
عدد 1 یعنی قابل جوشکاری در تمامی حالات
عدد 2 قابل جوشکاری در تمامی حالات به استثنای عمودی سرازیر
عدد 3 یعنی جوشکاری لب به لب و گوشه ای تخت و گوشه ای افقی
عدد 4 یعنی جوشکاری در حالات لب به لب و گوشه ای تخت خواهد بود
4- طبقه بندی الکترودهای ایرانی:
در مورد طبقه بندی الکترودهای ایرانی می توان به نحوه طبقه بندی الکترودهای ساخت کارخانجات الکترودسازی آما اکتفا کرد. الکترودهای متنوعی که در این کرخانجات ساخته میشوند بصورت خال رنگهای مختلف در انتها و کناره انتهایی الکترودها تقسیم بندی گردیده اند.
الف- الکترودهای سلولزی برای فولادهای غیر آلیاژی:
ب- الکترودهای روتایلی برای فولادهای غیر آلیاژی:
ج- الکترودهای آهکی برای فولادهایی با مقاومت کششی بالا و غیر آلیاژی:
د- الکترودهای کم آلیاژی برای فولادهای با مقاومت کششی زیاد و فولادهای مخصوص:
ه- الکترودهای جوشکاری کم آلیاژ و مقاوم در برابر حرارت:
شناسایی الکترودها بوسیله رنگ:
الکترودها را علائم حک شده روی جعبه آنها و یا بوسیله رنگی که در سطح مقطع الکترود و یا بصورت خال در قسمت بدون پوشش آن گذاشته میشود شناسایی میکنند.
مقایسه الکترود های پوشش دار و بدون پوشش:
برای اگاهی از اهمیت انواع پوشش های مختلف شیمیایی الکترودها ، ذیلا الکترودهای پوشش دار با الکترودهای بدون پوشش در بعضی از موارد مقایسه می گردند:
انتخاب الکترود مناسب:
انتخاب نوع الکترود علاوه بر نوع جریان مصرفی به عوامل زیر بستگی دارد:
1- کیفیت محل جوش
2- ترکیب شیمیایی فلز مبنا
3- وضعیت جوشکاری: الکترودهایی که برای جوشکاری در حالات عمودی یا بالای سر انتخاب میشوند انواع آنها به مراتب محدودتر از جوشکاری در حالات تخت و افقی می باشد.
4- شرایط کاربردی یعنی اینکه نوع الکترودهایی که برای ظاهر تمیز بکار برده میشود با الکترودی که برای استحکام زیاد بکار برده میشود متفاوت خواهد بود.
5- میزان نفوذ یا عمق نفوذ جوش در قطعه کار
6- هزینه جوشکاری
7- مهارت جوشکار
گاهی اوقات علاوه بر نوع الکترود اندازه الکترود نیز از نظر اقتصادی و سرعت عمل جوشکاری حائز اهمیت است.
الکترودهای ذغالی:
جوشکاری با الکترود ذغالی:
با وجود اینکه روشهای جوشکاری با الکترودهای فلزی مورد استعمال بیشتری دارند اما در بعضی موارد استفاده از الکترودهای ذغالی مزایای بیشتری را دارا می باشند.
جوشکاری با الکترود ذغالی چیست؟
جوشکاری با الکترود ذغالی فرایندی است که در آن عمل ذوب بوسیله حرارت ایجاد شده از قوس الکتریکی که بین الکترود ذغالی و قطعه کار ایجاد میشود انجام میشود. قوس ایجاد شده بوسیله الکترود ذغالی فقط به عنوان یک منبع حرارتی انجام وظیفه می کند. برخلاف جوشکاری با الکترودهای فلزی که در آن قوس الکتریکی فلز مذاب الکترود را روی کار منتقل می کرد، در اینجا خود الکترود اصولأ ذوب نمیشود. اگر برای فلز جوش دادنی به فلز جوش زیادی احتیاج باشد در این صورت از سیم جوش استفاده میشود. این سیم جوش بوسیله حرارت قوس الکتریکی ذوب شده و درز قطعه کار را پر میکند.
جوشکاری بوسیله الکترود ذغالی و با جریان مستقیم:
تمام ماشینهای جریان مستقیم که برای جوشکاری ساخته شده اند می توانند جریان لازم برای جوشکاری با الکترود ذغالی را تأمین کنند. برای اینکه نتیجه رضایت بخش تری بدست آید بهتر است از ژنراتور با ولتاژ زیاد استفاده شود زیرا در این روش به جوشکاری با قوس بیشتری نیاز داریم.
مقدار شدت جریان: انتخاب قطر الکترود بسته به شدت جریانی دارد که برای انجام کار مورد نیاز است و نیز مقدار شدت جریان بستگی به ضخامت صفحات فلزی جوش دادنی دارد. در هر صورت پس از انتخاب صحیح شدت جریان باید قبلا مقداری تمرین کرد و ضمن تمرین مشاهده خواهد شد که اگر شدت جریان زیاد باشد نوک الکترود به سرعت می سوزد و فلز جوش دادنی نیز به شدت گرم میشود. اگر نوک الکترود گداخته بیشتر از یک چهارم اینچ باشد نشان دهنده شدت جریان بیش از مورد نیاز می باشد.
چنانچه شدت جریان صحیح انتخاب شود قوس الکتریکی مرتب و ارام و پیوسته خواهد بود
انتخاب قطب: برای انجام جش با الکترود ذغالی بوسیله ماشینهای جریان مستقیم باید از قطب مستقیم ژنراتور استفاده کرد. اگر ماشینی که تعویق قطب نداشته باشد مورد استفاده قرار گیرد باید مطمئن بود که انبر جوشکاری به قطب منفی و فلز مبنا به قطب مثبت جریان وصل شده اند استفاده از قطب معکوس نه تنها باعث نامنظم بودن قوس الکتریکی میشود بلکه مقداری از ذرات ذغالی وارد فلز مذاب شده و به آن خاصیت شکنندگی می دهد. جنس سیم جوش باید با جنس فلز مبنا یکی باشد.
جوشکاری بوسیله الکترودهای ذغالی و ماشینهای جریان متناوب:
در این جوشکاری به انبرهای ویژه ای نیاز می باشد که مخصوص این کار ساخته شده اند انبر به الکترود ذغالی احتیاج دارد در جوشکاری با ماشینهای جریان مستقیم قوس الکتریکی بین الکترود ذغالی و فلز مبنا برقرار میشود و به محض اینکه الکترود را از قطعه کار دور کنیم شعله جوشکاری قطع می شود اما در جوشکاری با جریان متناوب قوس الکتریکی بین دو الکترود ذغالی ایجاد میشود اگر این الکترودها را از قطعه جوش دادنی دور کنیم باز قوس الکتریکی برقرار می ماند انتخاب قطر الکترودها در این نوع جوشکاری بستگی به نوع کار دارد.
روش انجام کار با دستگاههای جریان متناوب همان است که برای دستگاههای جریان مستقیم گفته شد. برای برقرار کردن قوس الکتریکی دو الکترود را به هم نزدیک میکنند تا قوس الکتریکی بین آنها برقرار شود. کنترل قوس الکتریکی بوسیله فشار آوردن جوشکار روی پیچ مخصوص انجام می گیرد. موقعی که فاصله صحیح و مناسبی بین دو الکترود بوجود آید. شعله منظم و آرامی برقرار خواهد شد و به تدریج که نوک الکترود می سوزد باید فشار وارد بر روی پیچ نیز افزایش یابد تا فاصله بین الکترودها ثابت بماند. موقعی که الکترودها می سوزند ایجاد قوس الکتریکی بین آنها امکان پذیر نمیشود در این موقع باید کار را متوقف کرد و فاصله الکترودها را مجددأ تنظیم کرد.
انبرهای جوش در الکترودهای ذغالی:
انبرهای معمولی که در جوشکاری با الکترودهای فلزی مورد استفاده قرار می گیرند برای جوشکاری با الکترودهای ذغالی مناسب نیستند زیرا الکترود ذغالی در اثر عبور جریان گرم شده و انبرهای معمولی را از بین می برند. برای اینکه از سوختن دست جوشکار جلوگیری شود دسته انبر الکترود ذغالی طوری ساخته میشوند که بوسیله هوا خنک شوند و در مواقعی که کارهای زیاد و مداوم با این روش جوشکاری مورد نظر باشد معمولا از انبرهایی استفاده میشود که دسته آنها بوسیله جریان آب خنک میشوند.
انواع الکترودهای ذغالی:
برای جوشکاری با الکترودهای ذغالی دو نوع الکترود ساخته شده است که یکی از گرافیت خالص و دیگری از ذغال پخته است الکترودهایی که با ذغال خالص ساخته میشوند در مقابل جریانهای زیاد جوشکاری دارای دوام بیشتری هستند اما قیمت آنها گران بوده و از نظر اقتصادی مقرون به صرفه نیستند. الکترودهای ذغالی باید بصورت مخروطی ناقص تراشیده شوند و قطر آنها باید برابر ضخامت فلز جوش دادنی باشند. قطر نوک الکترود باید بین 5/1 الی 2 میلی متر و طول قسمت تراشیده شده آن 16 الی 20 میلی متر باشد.
نکاتی که در این نوع جوشکاری با الکترودهای ذغالی باید مورد توجه قرار گیرند:
1-از انبرهای معمولی در این نوع جوشکاری نباید استفاده کرد.
2- برای اغلب کارهای جوشکاری باید از الکترودهای ذغالی پخته استفاده شود.
3- قطر الکترودها باید تقریبأ برابر ضخامت صفحات جوش دادنی باشند.
4- سیم جوش اضافه چنانچه مورد مصرف قرار گیرد باید جنس آن با جنس فلز مبنا مطابقت داشته باشد.
5- طول قوس الکتریکی حدود 3 الی 4 برابر ضخامت صفحات جوش دادنی انتخاب شود.